Our Craftsmanship
The manufacture of high quality Goodyear welted shoes remains very labour-intensive, requiring a highly skilled workforce to carry out more than 200 separate operations during an 8 week period. This method, originated by hand-makers centuries ago, gives the shoes an exceptional degree of strength, durability and comfort in wear.
The Good year welted process spans several production departments, each necessitating a multitude of different skills and experiences to ensure the shoes are completed to our exacting standards. Many of the operations, relying on excellent hand-eye co-ordination, take years to learn and a lifetime to master.
Stage One
Pattern Cutting
Once a design or style is agreed on by our Managing Director, it is discussed with our Pattern Cutters. Pattern cutting is the initial design and development phase and as any established Pattern Cutter will tell you, “If a pattern is not perfect when it leaves our pattern room, the shoes will not be perfect when they leave our factory.”
Once the patterns have been taken from the last, a prototype sample is made and test fitted. After any necessary adjustments to the patterns, a final sample pair is produced. It is crucial to ensure that the patterns fit correctly and that the upper sits nicely on the ‘wood’ (last) before starting on bulk production.
A Pattern Cutter’s work can be appreciated throughout the early stages of production, from the upper and lining patterns that a Clicker will use to the press knives needed in the Preparation department. A pattern cutter’s role is to reproduce the fundamentals of our lasts, enabling our craftsmen and women to make the shoes as they were intended to be.
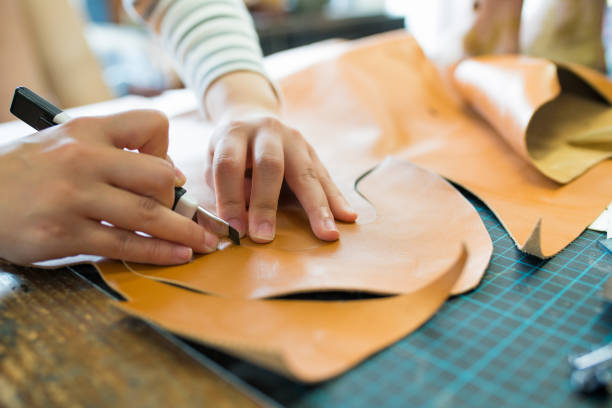
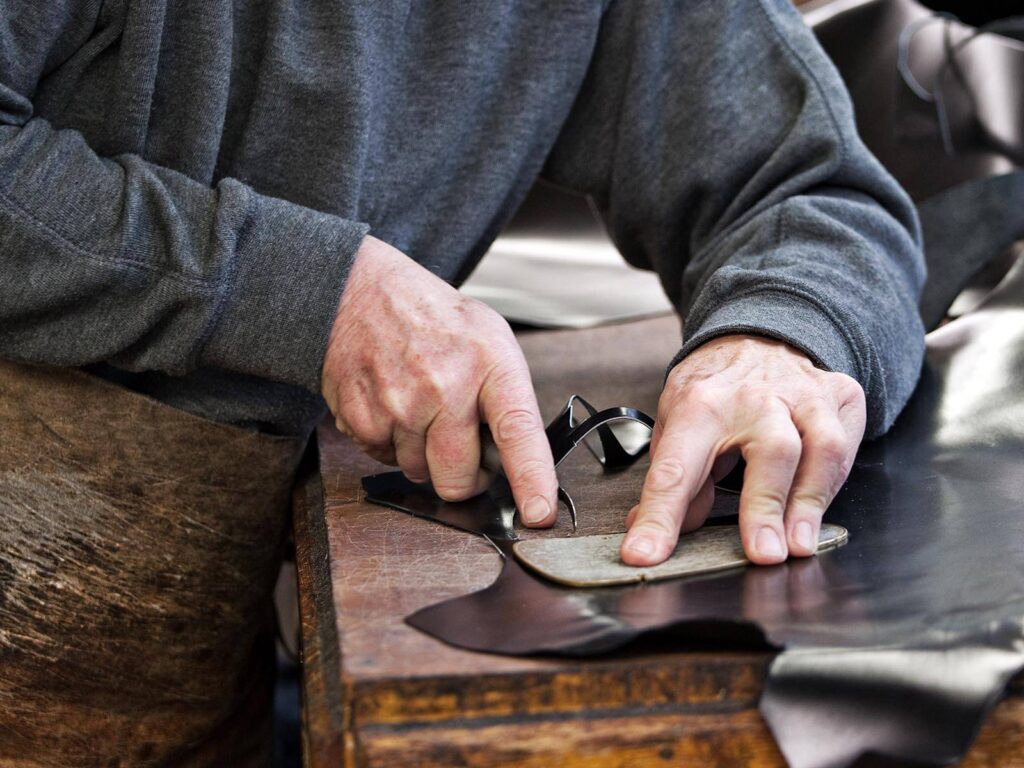
Stage Two
Clicking
With the leather stores bursting at the seams with high quality European calf, grain and suede, the clickers are eagerly poised with their knives at the ready. But not just any old knives…
The Clicking Department is the first stage of production where the shoe’s uppers are cut. The ‘Clicker’ is a highly skilled operative, whose name derives from the ‘click’ sound made when the knife is removed from the leather. Today, the department is a mixture of experienced hands and trainees. The younger members begin cutting lining leather, leaving the experienced clickers to focus on cutting the upper leather, whilst slowly passing on their years of expertise.
A Clicker’s main responsibility is to examine the leather for defects and to ensure these are not included in the shoes. Leather defects can be found in the form of barbed wire or disease scars, growth marks or veins. An experienced Clicker needs to be knowledgeable and highly skilled, in order to maximize the usage whilst retaining the utmost quality.A Clicker’s main responsibility is to examine the leather for defects and to ensure these are not included in the shoes. Leather defects can be found in the form of barbed wire or disease scars, growth marks or veins. An experienced Clicker needs to be knowledgeable and highly skilled, in order to maximize the usage whilst retaining the utmost quality.
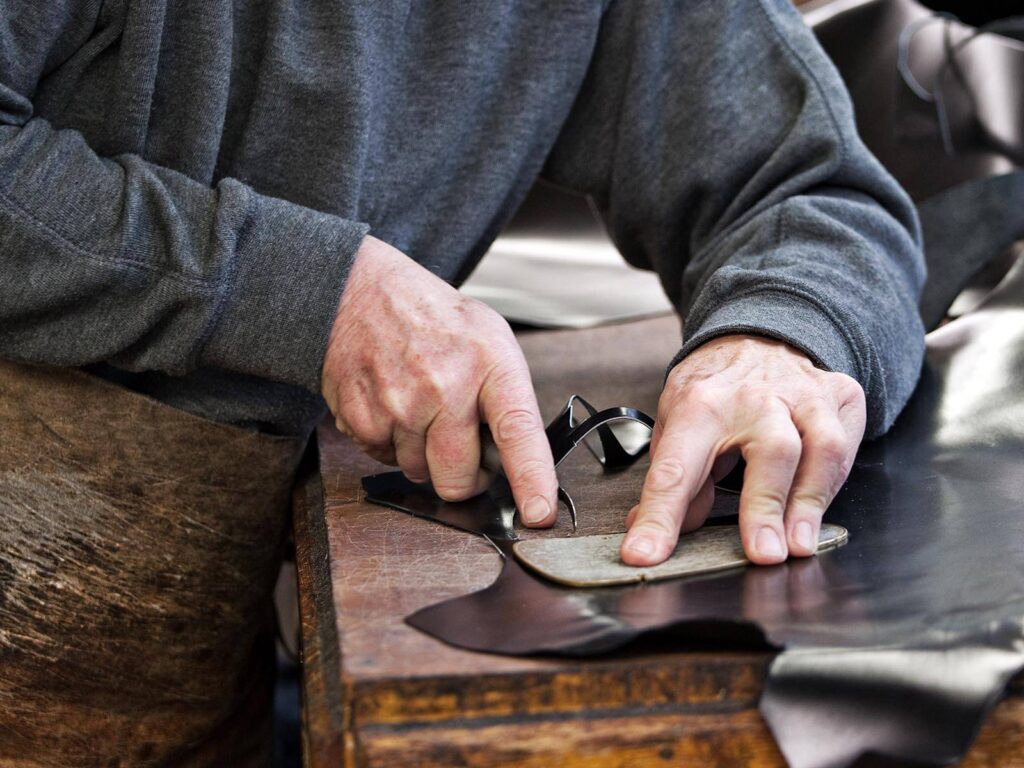
Stage Three
Closing
The Closing Room has over 100 members of staff, a busy department indeed. More operations can be found in this department than any other in the factory, each one of them requiring dexterity and patience.
At the next stage of production, the uppers are ‘closed’. Closing involves many different operations such as, punching holes for brogue styles, raw edge staining, hand-sewing, machine stitching pre-prepared sections together to form the upper and fitting eyelets. The Closing Room machinists are highly skilled requiring excellent hand and eye coordination.
To put into context how niche a profession Hand Stitching is, Jaguar Luxe relies on just one. Ned. Ned is a marvel to sit and appreciate, giving you time to truly understand the rarity value of his work.
Ned uses a 40+ year old curved awl to precisely make multiple stitch holes ensuring that he does not pierce the full substance of the material (therefore concealing the stitch). He then feeds a piano wire, to which he attaches a wax thread (which he also creates), through each hole, producing a hand tightened cross-stitch. It is painstaking work, that
results in a hand stitched upper of the highest regard.
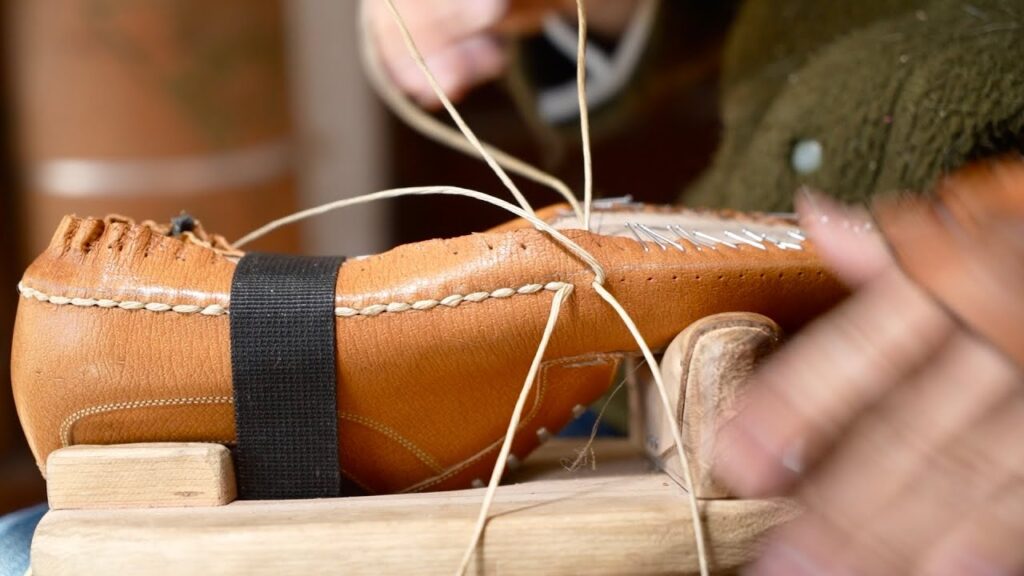
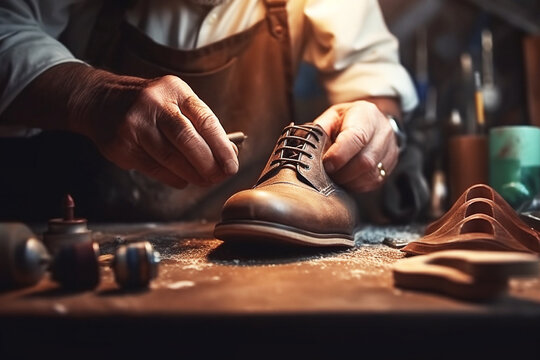
Stage Four
Preparation
Preparation refers to the gathering of all other components that are required during the making of our shoes. In typical form, many of the components are produced in-house, including the cutting of heels, insoles and soles. The heel department and sole department are small workshops in their own right and work tirelessly to feed the
factory beside them.
Preparation of the ‘bottom’ part of the shoes is the fourth stage of production. The insoles and soles are cut from leather bends or rubber sheets using large heavy presses.
The leather insoles are prepared for ‘Lasting’ by attaching the material rib, to which the welt will eventually be stitched. The heels are built in-house with leather or rubber lifts and top pieces. At this stage the appropriate lasts are selected to be matched with the
closed uppers.
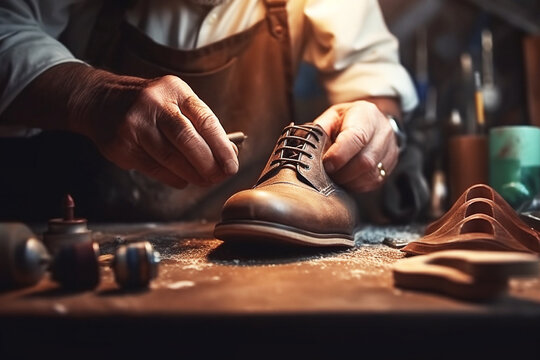
Stage Five
Lasting
Jaguar Luxe uses the term ‘Lasting’ to refer to ‘pulling the upper over the last’ thereby giving shape to the shoes. The last is a shoemaker’s foundation, and can be thought of as their most closely guarded secret. With heritage paving the way for the exceptional last development, Jaguar Luxe are continually developing new lasts.
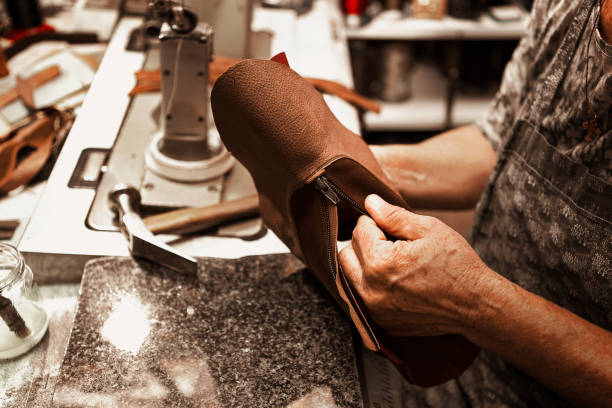
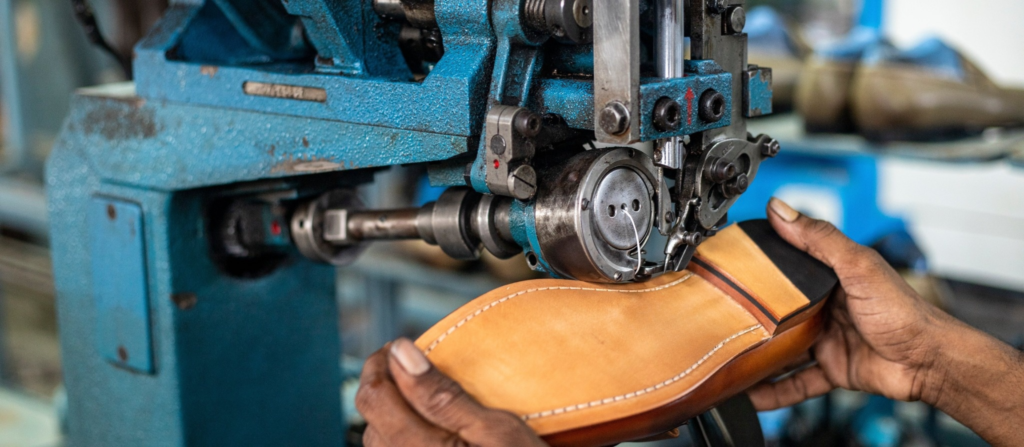
Stage Six
Making
Making is where you will find the famed ‘Goodyear-welting’ stitching machines. As the first shoe factory this side of the Atlantic, to install the latest version of a welt sewing machine, the ever industrious Messrs. Jaguar Luxe were able to scale up production to 500 pairs per day.
An important process in this department is ‘Welt Sewing’ where the operative stitches the welt (a strip of leather) to the rib that has been attached to the insoles. The welt is a
key element in the Goodyear-welted process. The bottoms of the shoes are filled with cork and wooden shanks are inserted to provide support beneath the insoles. The soles
are then stitched to the welt. This method allows for the soles to be removed for repair without affecting the uppers. After the soles have been attached the shoes undergo a process called ‘Bottom Levelling’, which rounds the soles to the shape of the last.
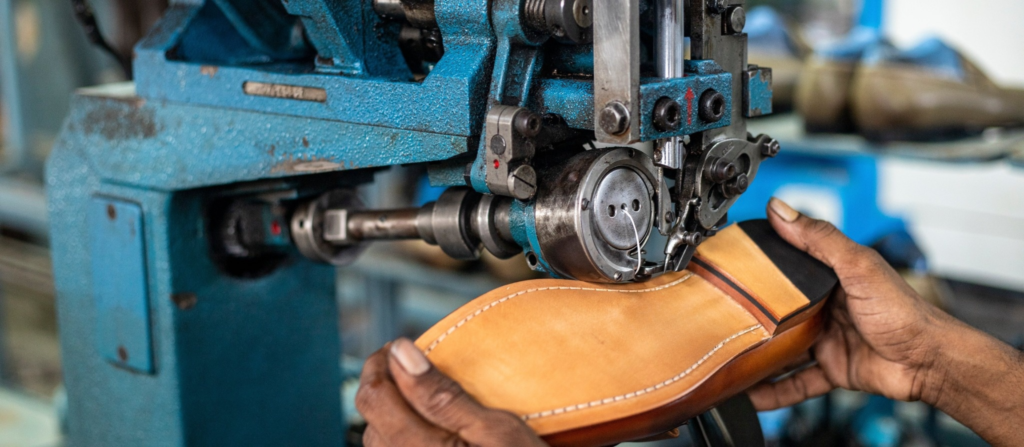
Stage Seven
Finishing
Craftsmanship is now in full flow and mistakes are costly. The Finishing Room is where a team of finishers are cleaning, preparing and adding the finishing touches to the soles, that Jaguar Luxe customers appreciate so greatly.
In the Finishing Department, the heels are attached, trimmed and then scoured with emery paper for a smooth finish. Edge trimming is the next highly skilled process,
whereby the sole edges are trimmed to the specific shape of the last. This is done ‘free-hand’ like many other operations in Goodyear-welted shoe making. The soles and heels are then stained and hot wax is applied to the edges to provide a waterproof seal and a good shine. Various decorative finishes are applied to the soles, such as wheeling and crowing, before a final polish.
The aesthetic arena that is the Finishing Department provides some of the finer details that can be appreciated on a pair of Jaguar Luxe shoes. Wheeling & Crowing, Top Ironing and a Gentleman’s Corner are just some of our trademark features.
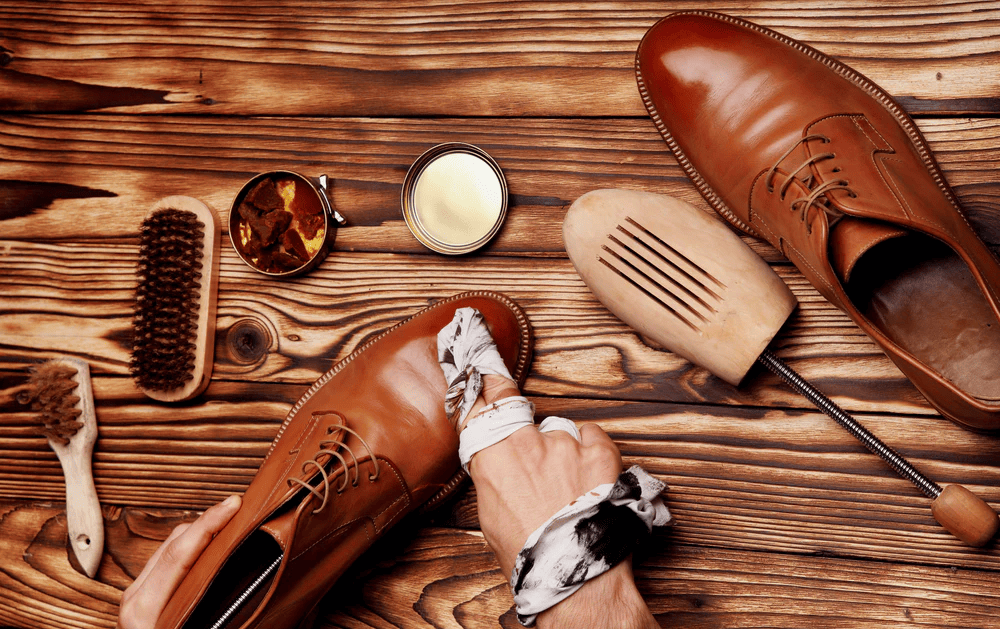